For e-commerce entrepreneurs, especially those managing Amazon FBA or launching private-label products, supplier selection is a mission-critical decision. One wrong move can lead to delayed launches, inventory loss, or worse—brand damage. That’s where factory audits come in.
This guide explains the factory audit meaning, outlines audit requirements, breaks down the five key audit checklists, explores different types of factory audits, and answers the crucial question: how much does a factory audit cost?
What Is a Factory Audit?
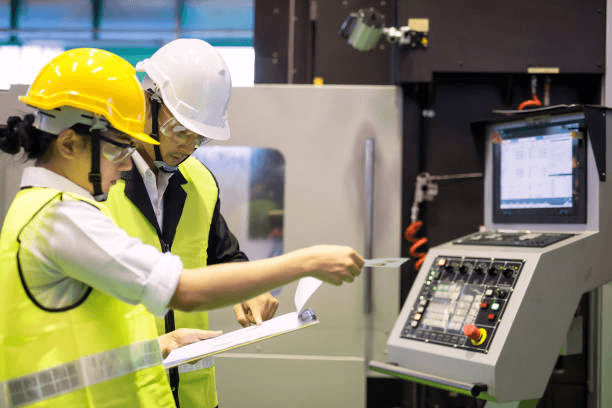
A factory audit is a structured evaluation of a supplier’s systems, processes, and environment. It’s conducted to assess whether a factory can produce goods according to your quality standards, ethical expectations, and compliance requirements.
This isn’t just a “visit.” It’s a tool to eliminate sourcing risks, often performed before the first order is placed or periodically for ongoing compliance.
Why Importers Rely on Factory Audits
- Validates supplier credibility
Confirm if the business is real, properly registered, and operating legally.
- Verifies quality systems
Understand how the factory monitors and maintains product quality across production cycles.
- Protects brand reputation
Avoid failed shipments, unsafe products, or human rights violations tied to your name.
- Informs negotiations
Use audit findings to negotiate terms, set clear expectations, or decide to walk away.
- Strengthens buyer leverage
Audits show suppliers you’re serious and professional—making them less likely to cut corners.
What Are the Requirements for a Factory Audit?

Before an audit takes place, both parties must be properly prepared. The following are essential conditions to ensure a smooth, efficient process.
Pre-Approval from the Factory
A successful audit begins with clear communication and agreement from the supplier.
- Written consent
The factory must allow inspectors to enter the facility and review internal processes.
- No-obstruction policy
They must not interfere with the audit or restrict access to certain areas.
- Cooperation commitment
Staff should be made available to answer questions and provide documentation.
- Transparency mindset
A factory unwilling to participate openly is a clear red flag.
Defined Audit Scope and Standards
Clarify what the audit will cover and which standards or guidelines will be used.
- Audit type
Determine whether the focus is on quality, social responsibility, environmental safety, or all three.
- International standards
Audits often reference ISO 9001 (quality), SA8000 (social), or WRAP (workplace compliance).
- Customized checklists
For Amazon FBA sellers, packaging and labeling compliance should be part of the audit scope.
Documentation Preparedness
A large portion of the audit involves checking paperwork.
- Business licenses and permits
Verify if the factory is legally registered and licensed for export.
- Quality manuals and SOPs
These show how the factory controls production processes.
- Employee records
Review contracts, age verification, and payroll to assess labor compliance.
- Certificates and audit history
Factories may present prior audit results or certifications.
- Production logs
These help verify capacity claims and consistency.
Accessibility to Key Areas
The audit will not be meaningful unless all relevant areas are accessible.
- Production floor
Auditors need to observe actual workflows and machines in use.
- Warehousing and storage
Check how raw materials and finished goods are handled.
- Testing labs
Inspect internal quality control mechanisms, including tools and protocols.
- Worker amenities
If workers live on-site, dorms and canteens should be inspected for health and safety.
Use of Qualified Auditors
The quality of an audit depends heavily on the auditor’s expertise.
- Experienced professionals
Auditors must be trained in ISO or compliance frameworks.
- On-ground teams
Local experts understand cultural nuances and typical factory tricks.
- Multilingual ability
Communication is smoother when the auditor speaks the local language.
- Reporting skills
Post-audit documentation should include photos, severity scores, and action plans.
The Five Core Audit Checklists
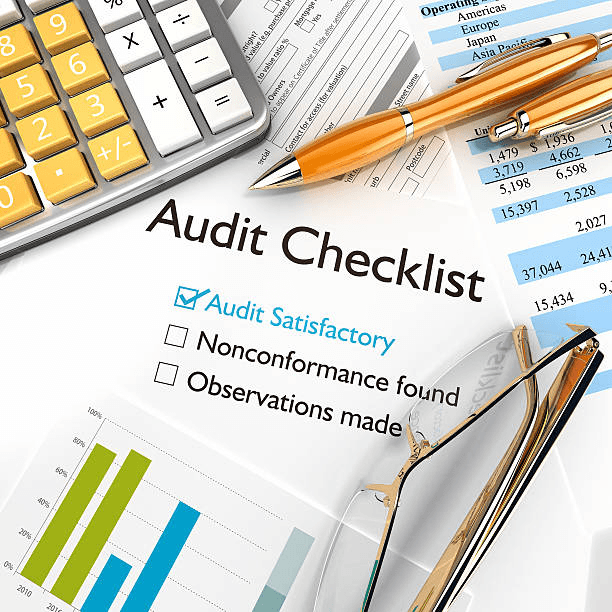
Factory audits typically follow five core checklists that evaluate the supplier from multiple dimensions.
Quality Management System (QMS)
This section assesses how the factory ensures consistent product quality.
- Standard Operating Procedures (SOPs): Are there documented steps for each production process?
- Defect tracking: How are production issues identified and resolved?
- In-process inspections: Are there quality checks at different production stages?
- Testing capabilities: Is there equipment for product safety or durability tests?
- Training programs: Are workers trained to maintain quality standards?
Manufacturing Capacity and Capabilities
This determines if the supplier can meet your volume and timeline expectations.
- Production volume data: Can the factory handle your order size within deadlines?
- Machinery and maintenance: Are machines modern, and are maintenance records available?
- Staffing levels: Is there enough skilled labor to support your project scale?
- Production bottlenecks: Any visible weaknesses that could delay timelines?
- Outsourcing activities: Are any steps subcontracted without disclosure?
Social and Labor Conditions
This section checks if the factory complies with local labor laws and ethical standards.
- Child labor and age verification: Are all workers of legal age?
- Wage and hour compliance: Are wages fair, and is overtime voluntary and paid?
- Safety measures: Fire extinguishers, exits, drills, and protective equipment in place?
- Worker housing: Dormitories should be clean, ventilated, and secure.
- Worker interviews: Anonymous interviews provide insights beyond what managers report.
Environmental Management
Factories should minimize negative impacts on the environment.
- Waste disposal practices: Are hazardous materials safely managed?
- Efficacité énergétique: Are there energy-saving initiatives or eco-conscious programs?
- Use of banned substances: Are restricted chemicals like lead or mercury used?
- Water management: Is there a wastewater treatment system?
- Environmental permits: Are licenses and environmental audits up-to-date?
Facility Security and Export Readiness
Especially relevant for Amazon or U.S. importers, this checklist ensures export compliance.
- Inventory control: Is stock managed with accuracy and traceability?
- Packing areas: Clean, organized, and meeting buyer requirements?
- Customs documentation: Are export forms, HS codes, and invoices handled properly?
- Transport access: Can trucks or containers access the facility without delay?
- Anti-theft measures: Fences, cameras, guards, and controlled access points?
Types of Factory Audits
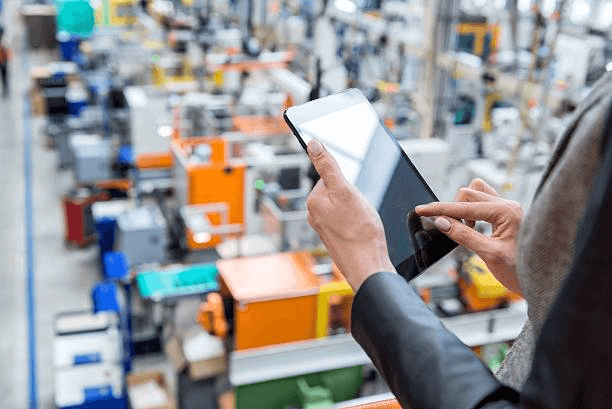
Choosing the right audit type depends on your goals, product category, and level of risk.
Initial Capability Audit
Ideal before placing your first order. Assesses legitimacy, size, and basic capacity.
- Helps you avoid fake factories or middlemen.
- Focuses on legal documents, basic production capabilities, and facility size.
- Can be completed in 1 day by local inspectors.
Quality System Audit
Recommended for buyers focused on consistency and brand reputation.
- Evaluates internal controls to detect and correct defects.
- Includes inspection of raw materials, finished goods, and testing procedures.
- Ensures ISO 9001 or similar systems are in place.
Social Compliance Audit
Critical for Amazon sellers or retailers concerned with ethical sourcing.
- Assesses labor conditions, safety, and management practices.
- Uses international frameworks like SA8000 or BSCI.
- Includes worker interviews and documentation reviews.
Environmental Audit
Suited for brands promoting sustainability.
- Reviews energy, emissions, waste, and chemical handling.
- Verifies eco-certifications and local compliance.
- Can help you meet corporate sustainability reporting (CSR) targets.
How Much Does a Factory Audit Cost?
Average Price Ranges
Costs vary depending on the depth of the audit and the location of the factory.
Audit Type | Typical Cost Range |
Basic Factory Verification | $300–$500 |
Standard Quality Audit | $800–$1,200 |
Social or Environmental Audit | $1,000–$1,800 |
Multi-Day / Multi-Site Audit | $2,000+ |
Factors That Influence the Cost
- Audit Scope: A simple legal check costs far less than a full ISO audit.
- Emplacement: Remote regions may incur travel surcharges.
- Agency Used: Top firms like SGS charge more than local freelance inspectors.
- Urgency: Express audits can come with a 20–30% premium.
- Report Detail: Detailed reports with photos, scoring, and recommendations cost more—but are worth it.
Final Thoughts: Make Audits Work for You
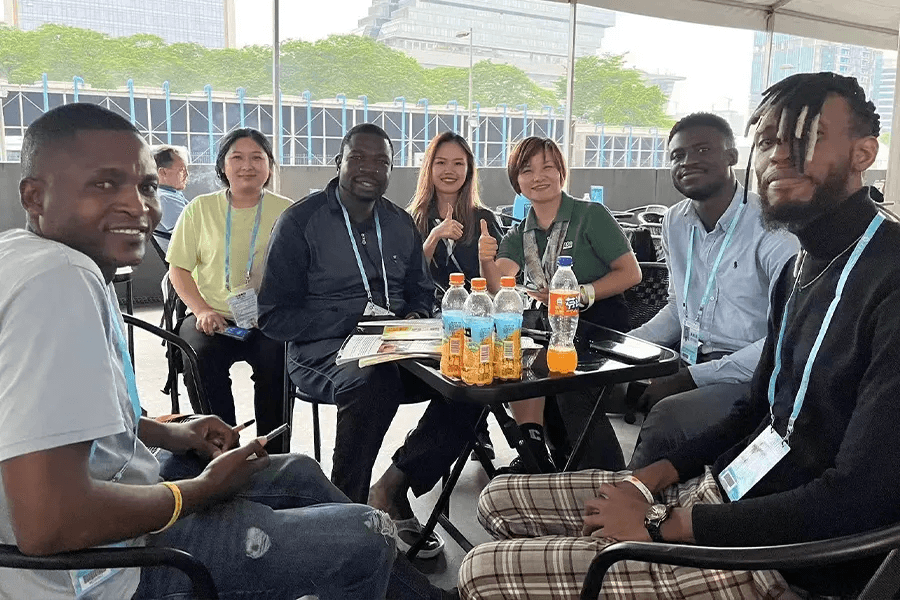
For time-strapped importers, a factory audit is your frontline defense against delays, defects, and scams. It helps you avoid working with unverified suppliers and gives you data-driven confidence in your sourcing decisions.
Whether you need a one-time inspection or ongoing compliance checks, factory audits turn guesswork into guaranteed results.
Need help scheduling a reliable audit in China?
Asian Sourcing Group offers on-the-ground factory vetting, in-depth audit reports, and FBA-ready compliance checks with real-time project tracking.
👉 Get your first audit quote within 24 hours.